In the pharmaceutical industry, nitrogen is essential for maintaining the safety and effectiveness of medications. Nitrogen gas, used throughout the development and production stages, plays a key role in stabilizing active ingredients and extending the shelf life of products like tablets and injectables. With strict quality and safety requirements, the industry benefits from advanced nitrogen generation technologies, such as membrane and PSA systems. These systems provide a reliable and efficient supply of nitrogen directly on-site, allowing optimal purity and volume control crucial for pharmaceutical manufacturing.
Every time one reaches for a medication, whether it’s a simple antibiotic or a complex medicine used for a chronic disease, there’s an invisible protector behind its safety and effectiveness: nitrogen.
Nitrogen gas is a vital component in the pharmaceutical industry in both stages of medicine development and production. Its properties help in maintaining the integrity, efficacy, and safety of pharmaceutical products. From stabilizing active pharmaceutical ingredients to ensuring the longevity of finished products like tablets and injectables.
Due to high standards for product quality and safety required in the industry, the role of nitrogen becomes even more critical. It is therefore important to understand the various roles nitrogen plays in achieving these objectives. Knowing that the supply methods of nitrogen may vary, it equally important to highlight the different methods and the advantages and disadvantages they offer.
The use of membrane and PSA (Pressure Swing Adsorption) nitrogen generators represents an important advancement, providing reliable and efficient nitrogen supply directly tailored to the needs of pharmaceutical production. Onsite nitrogen generation ensures on-demand supply with complete control over purity and volume.
Forms of nitrogen used in pharma: Gas vs. Liquid
In the pharmaceutical industry, nitrogen is used in two main forms: gas and liquid. Nitrogen gas, often produced on-site with PSA or membrane generators, or supplied through cylinders and bulk delivery is essential for protecting sensitive products during manufacturing by preventing oxidation. Liquid nitrogen, known for its rapid freezing capabilities, is used mainly in preparatory steps for processes like lyophilization. While nitrogen gas is integral to various manufacturing stages, liquid nitrogen’s use is more specialized, supporting initial freezing needs across different industries, including food and beverages.
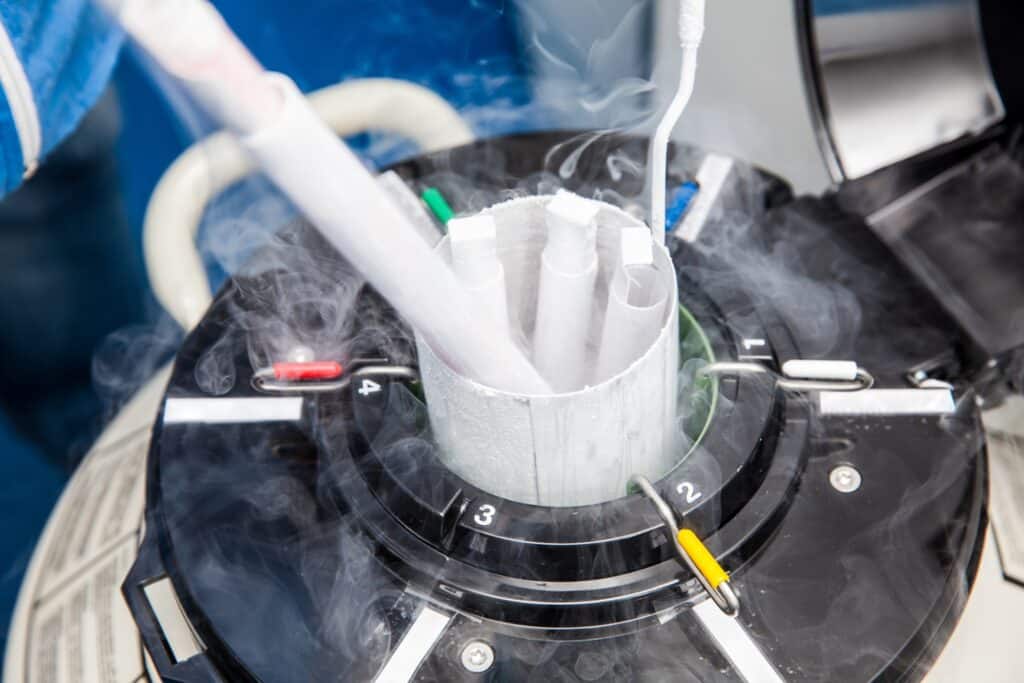
Applications of nitrogen in the pharmaceutical industry
Nitrogen gas is the prime element across both stages of pharmaceutical development and production. As in many other industries such as food and beverage, marine, mining etc. it plays a very important role for maintaining the integrity, efficacy, and safety of products. In pharma, its applications span from manufacturing processes to preservation techniques.
- Manufacturing:
Inerting and Blanketing: Here, is nitrogen used to create a non-reactive environment in containers and production equipment, protecting oxygen-sensitive medications such as epinephrine from degradation.
Purging and Sparging: This process involves using nitrogen to eliminate dissolved oxygen in solutions during the manufacturing of sterile injectable drugs, reducing oxidation risk.
Freeze drying (Lyophilization): In the freeze-drying of biopharmaceuticals like vaccines, nitrogen aids in maintaining low pressure and temperature, essential for preserving the stability of these products.
Product transfer: Nitrogen acts as a carrier to move powdered drugs within production equipment, protecting them from damage that moisture and other impurities can cause.
- Preservation: Similarly, as in food and beverage industry, nitrogen is used for preservation and packaging for shelf-life extension
Controlled Atmosphere Storage (CAS): This method involves adjusting the storage environment’s atmospheric conditions, utilizing nitrogen to displace oxygen. It’s particularly beneficial for storing bulk drugs and raw materials, significantly slowing down degradation processes.
Modified Atmosphere Packaging (MAP): MAP involves adjusting the gas composition inside product packaging, often replacing oxygen with nitrogen to enhance shelf life. This technique is crucial for a wide range of pharmaceuticals, from pills to biologics. It allows for medication maintain its effectiveness and safety until they reach consumers.
The use of nitrogen gas, generated from PSA or membrane generators, or other methods of supply, and its application in both CAS and MAP techniques, highlights its important role in the pharmaceutical industry.
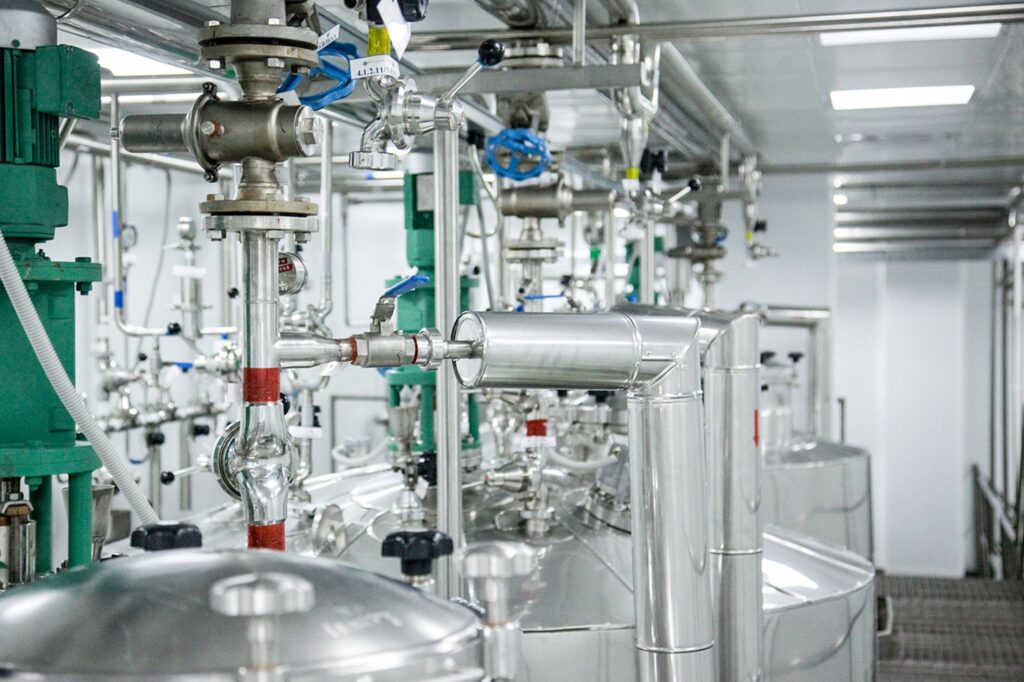
How the pharmaceutical industry supplies nitrogen?
There are three main methods of Nitrogen supply in the industry, they include:
- Cylinder Supply: Nitrogen gas can be delivered in high-pressure cylinders. This method is common for smaller scale or less frequent needs.
- On-site Nitrogen Generators: Pharmaceutical facilities may also opt for on-site nitrogen generation, using either Pressure Swing Adsorption (PSA) technology or membrane technology to produce nitrogen gas from the ambient air.
- Bulk Liquid Supply: For larger demands, nitrogen can be supplied in liquid form, stored in large tanks, and vaporized to gas when needed.
Advantages and disadvantages of different supply methods
Each supply method comes with its own set of advantages and disadvantages:
- Cylinder Supply
- Advantages: Convenient for small-scale applications; no need for large infrastructure.
- Disadvantages: Higher long-term costs; requires regular handling and replacement; has potential for supply disruptions.
- Bulk Liquid Supply
- Advantages: Suitable for high volume needs; more cost-effective than cylinders for large scale operations.
- Disadvantages: Requires significant space for storage; has potential for evaporation losses; infrastructure for vaporization needed.
- Nitrogen Generators
- Advantages: Unlimited supply; cost-effective in the long term; minimal handling and safety risks; environmentally friendly.
- Disadvantages: Initial investment can be high; requires regular maintenance.
On-site Nitrogen Generators: Membrane and PSA
To support the needs of the pharmaceutical industry with high-quality nitrogen, on-site nitrogen generators have become a fundamental in many manufacturing facilities. They offer a dependable and direct supply of nitrogen, crucial for various pharmaceutical applications. There are two principal technologies for on-site nitrogen generation: membrane and Pressure Swing Adsorption (PSA).
Membrane Nitrogen Generators
- Operation: These generators separate nitrogen from air through a semi-permeable membrane, allowing oxygen and other gases to pass through more quickly than nitrogen.
- Suitability: Best for applications needing nitrogen purity up to 99.5%, commonly used in packaging and quality control of medicines.
- Advantages: Known for simplicity, reliability, and low maintenance, membrane generators efficiently provide a continuous nitrogen supply and are scalable if large quantities are needed.
Pressure Swing Adsorption (PSA) nitrogen generators
- Operation: PSA generators use adsorbent material to capture oxygen from air, cyclically pressurizing and depressurizing to produce nitrogen gas.
- Suitability: Ideal for higher purity requirements, up to 99.999%, crucial for manufacturing processes that demand the highest quality atmosphere.
- Advantages: Offers high purity levels and is also scalable, making it suitable for larger operations that require precise control over nitrogen quality.
Benefits of using nitrogen generators
Nitrogen generators offer numerous benefits, they include:
- Cost Efficiency: Over time, the cost of generating nitrogen on-site is significantly lower than purchasing it in cylinders or in bulk liquid form.
- Reliability and Safety: On-site generation provides a consistent and reliable supply of nitrogen, reducing the risk of contamination and supply shortages.
- Environmental Sustainability: Generating nitrogen on-site reduces the carbon footprint associated with transporting cylinders or liquid nitrogen.
- Customization: Nitrogen generators can be tailored to meet the specific purity and flow rate requirements of different pharmaceutical applications.
Onsite nitrogen generation offers a greener, safer, and more cost-effective solution for the industry, eliminating the need for energy-intensive liquid nitrogen and high-pressure storage. The approach reduces the risk of injuries associated with handling and storage, and cuts nitrogen costs. Moreover, it ensures a reliable, on-demand supply with complete control over purity and volume, enhancing operational flexibility without the worry of market price fluctuations or delivery delays.
Efficiency in medicinal manufacturing with OXYMAT nitrogen generators
OXYMAT nitrogen generators stand at the forefront of on-site gas generation technology, offering pharmaceutical manufacturers a robust solution for their nitrogen needs. With state-of-the-art PSA or membrane technologies, OXYMAT systems are engineered for utmost efficiency.
Quality and durability are paramount in pharmaceutical manufacturing, and OXYMAT delivers on both fronts. These are the different models that OXYMAT offers to their customers:
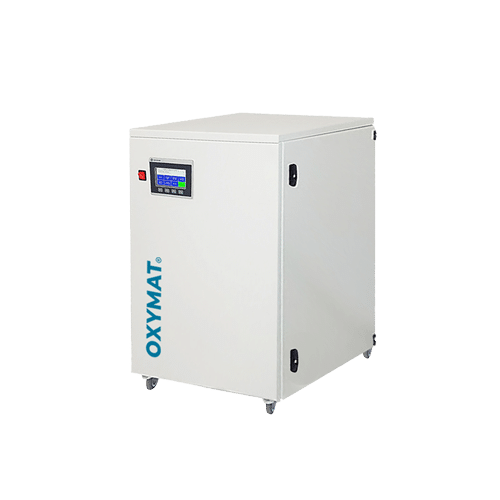
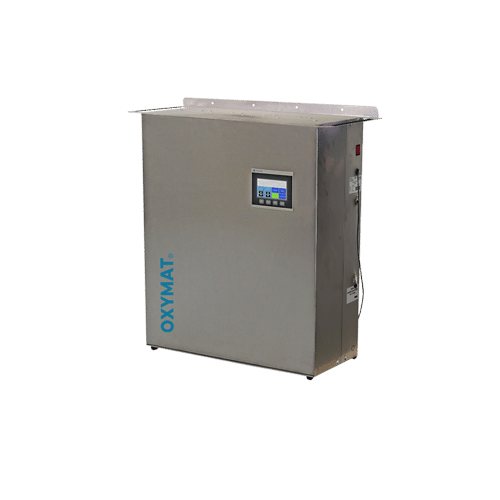
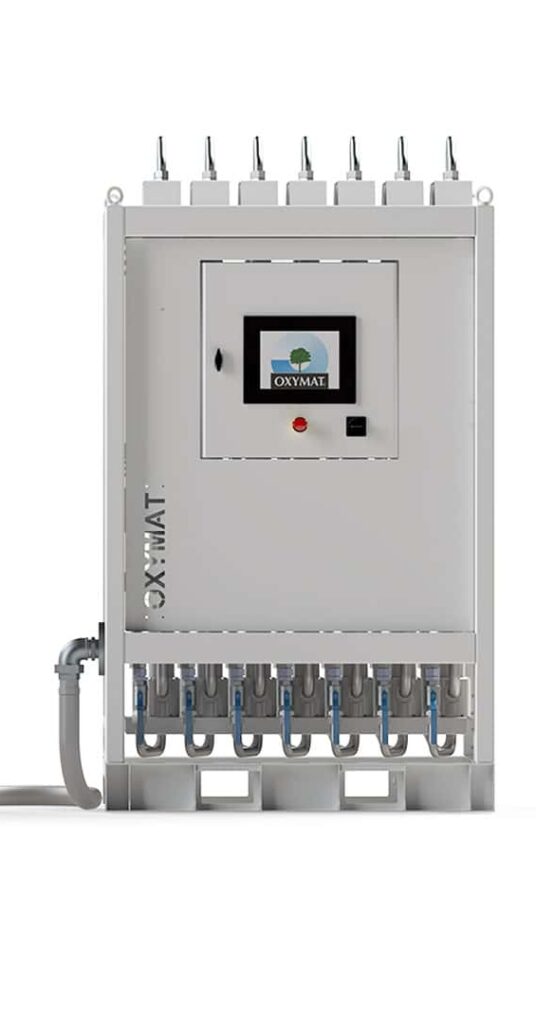
These generators are customizable to specific flow rates, purity levels, and pressures. Furthermore, OXYMAT’s solutions are scalable to grow alongside your manufacturing demands. The reliability of these systems, combined with their low maintenance requirements, ensures that pharmaceutical production lines remain uninterrupted, further underlining the operational advantages of on-site nitrogen generation. By adopting OXYMAT’s nitrogen generators, pharmaceutical facilities can expect not just significant cost savings over traditional nitrogen supply methods, but also a steadfast commitment to quality and environmental sustainability.
Conclusion
In conclusion, nitrogen’s basic role in the pharmaceutical industry cannot be overstated, from safeguarding the integrity of sensitive compounds to ensuring the efficacy of life-saving medications. The advancement of on-site nitrogen generation technologies, represented by membrane and PSA systems, marks a significant leap towards operational efficiency, reliability, and sustainability. With innovative solutions like OXYMAT PSA and membrane nitrogen generators, the pharmaceutical industry is well-equipped to meet the challenges of today and tomorrow, ensuring that high-quality, safe, and effective medications continue to be available to those in need. These technologies not only help in streamlining the production but also facilitate in the industry’s commitment to environmental sustainability and cost-effective manufacturing solutions.